EDCO Members Connect: Novunex Provides Metabolic Maintenance With Process Automation Platform
Manfred Walder of Novunex helped Metabolic Maintenance improve efficiency by 50% with their SaaS platform, leading to significant labor cost savings and plans for further automation.
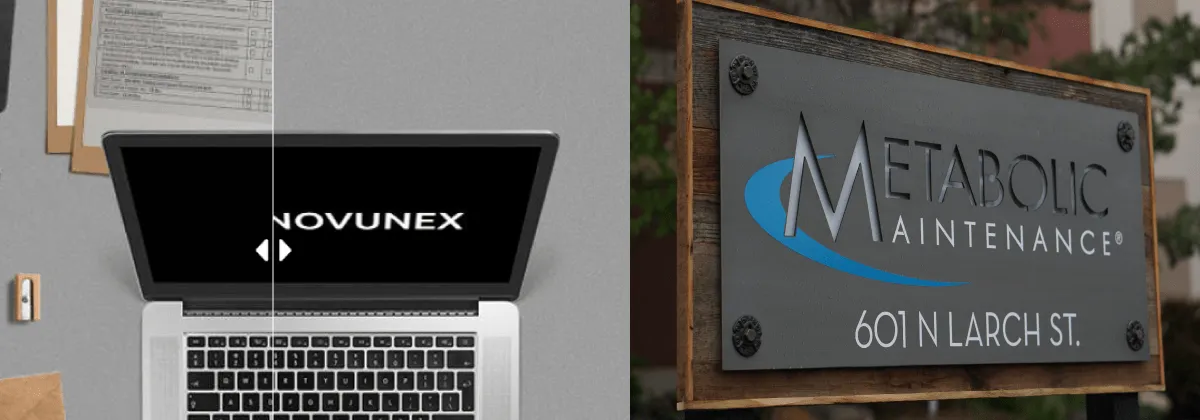
Bend, Ore. – May 29th, 2019: Meet Manfred Walder, VP of Operations for Novunex. Novunex is a highly configurable software as a service (SaaS) platform that manages business processes of all kinds. The pre-configured, industry proven method enables customers to get up and running within a day. Novunex provides customers startup and ongoing support including review and mapping of their current processes, alignment of the pre-configured models to the customer process and training. Metabolic Maintenance produces pure, high quality, preservative-free products with no added excipients, fillers or binders. Based in Sisters, Oregon, their products are manufactured per the highest standards with only the most conscientious sourcing of ingredients. It is the oldest family-owned company in the nutritional supplements industry. Hear from Jeff Minke, QA/QC Manager, about Metabolic Maintenance's experience using Novunex's process automation platform.
EDCO: How did Novunex help you to improve efficiency and compliance? JM: Novunex is a very robust software, that has a great amount of flexibility which allowed us to tailor it exactly to our process requirements. Metabolic Maintenance is currently using Novunex for one of our critical quality processes with the goal of reducing labor costs and time. Since using Novunex at Metabolic Maintenance, we have seen a 50% improvement in efficiency and labor cost savings. This experience has shown us a cost-efficient way to automate which is leading us to more opportunities to gain efficiencies as a company. Metabolic Maintenance is already planning the next processes that can be automated with Novunex to drive improvements in our operations. The team at Metabolic Maintenance is highly impressed by the functionality of Novunex and how easy it is to use. Because of the flexibility offered by Novunex, Metabolic Maintenance would strongly recommend this software.
EDCO: How did EDCO help in the selection process for a process automation platform and why did you select Novunex? JM: Metabolic Maintenance was introduced to Novunex by Jon Stark, REDI Sr. Director. Metabolic Maintenance was looking for a new innovative technology that could help improve efficiency and build upon current processes and procedures already in place. Jon directed us to Novunex and we could tell from the beginning we had made the right decision by working with Novunex.
EDCO: How has your experience been with the Novunex software? JM: Since Novunex was a brand-new software for Metabolic Maintenance, our team needed to see it in action. After a few reference visits with existing Novunex customers in Central Oregon, the Metabolic Maintenance staff was impressed by the efficiency and capability Novunex was able to offer. After approximately three months of planning and configuring the software to our specific needs, Novunex is used now in our day-to-day operations. Hear how Manfred is helping businesses like Metabolic Maintenance get ready for the future by saving time and cost with process automation done right.
EDCO: Why did you move to Central Oregon? MW: After moving from Austria to San Diego in 2001 it took me about 3 years to discover Bend. I felt immediately connected with the area and knew that this was the place I wanted to live. I was working for one of the biggest contract manufacturing companies, Flex, and I had to find a new opportunity to make a move to Bend possible. Finally, in 2006 I accepted a leadership position for developing and implementing a global quality management system for FlexMedical and was able to make my move to Bend. I continued working for Flex, and later for Zimmer as a telecommuter, before the perfect constellation of events led me to the start of our company, which I did together with two friends and former co-workers in 2015.
EDCO: How did you hear about EDCO? MW: Having always worked in factories and corporate environments, it was exciting but also very challenging to start my own business. I was living in Bend but I didn’t really know the support and infrastructure available for new businesses. My first PubTalk in May 2015 was a real eye-opener. Seeing and feeling the environment EDCO had created, gave me confidence that I was in the right place.
EDCO: How did EDCO help you? MW: In the early stages of our company, we got help from EDCO's Venture Catalyst, Brian Vierra, who connected us with a mentor and gave us the opportunity to pitch our company at a PubTalk. During EDCO events we made introductions to other business owners and operation managers from local businesses. I realized that it was difficult for EDCO Area Directors to explain what we are doing and how we help customers, therefore we scheduled some face to face meetings and customer visits to show them what we do. I believe that this educational part was important for the introduction to Metabolic Maintenance from Jon Stark, REDI Sr. Director. Jon understood what we could do and he saw the need Metabolic Maintenance had.
EDCO: How did this opportunity turn out for Novunex? MW: We had multiple meetings with the Metabolic Maintenance team to understand their pain points and goals. After creating a broad business process automation plan, which included inspection and lab management, product and recipe management and forecasting we presented the benefits of a digital transformation to the management team. In order to better visualize how our software helps GMP facilities (FDA - Good Manufacturing Practices) to be more efficient and compliant, we organized several reference visits which were supported by Caprielle Foote-Lewis, EDCO's Sisters Area Director. This detailed preparation work led to the first project which was kicked-off in February this year.
EDCO: Can you tell us more about the project? MW: The best part of every new project is learning about the customer and their very specific use cases and challenges. We recommended starting with a critical but less integrated part of the business process automation plan, which in this case was the inspection and lab management solution. To keep the project efficient, we used some of our preconfigured modules to start. In weekly sprints, we added features and refined the processes and dashboards to align them with the unique requirements. To create the perfect fit, we believe that software needs to precisely align with process requirements and support an efficient, effective and compliant execution.
Get Guided Support When You Bring Your Business to Central Oregon
The team at EDCO offers free business relocation services.
